CAUSTIC SODA FLAKING UNIT
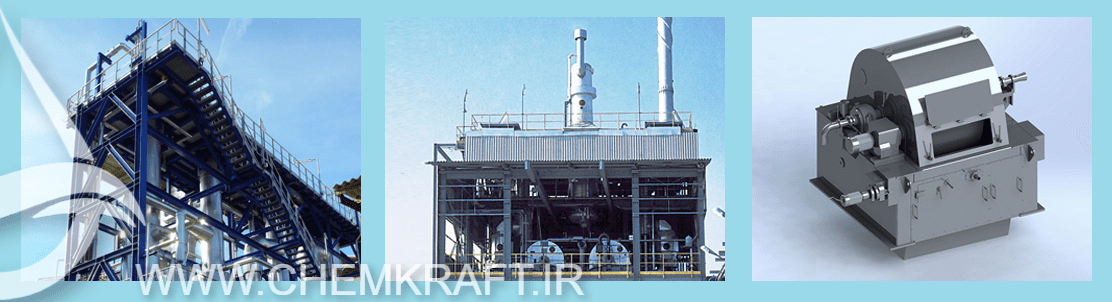
1. Introduction
The caustic soda flaking unit plays a crucial role in the production of high-quality caustic soda flakes, which are widely used in various industries such as chemical manufacturing, pulp and paper, textiles, and water treatment. This article provides a comprehensive description of the caustic soda flaking unit, exploring its process overview, equipment and machinery, operational parameters, safety measures, maintenance, environmental considerations, and future developments. Understanding the intricacies of the flaking unit is essential for ensuring efficient and safe production of caustic soda flakes, while also considering environmental sustainability and future advancements in the flaking process.
Caustic Soda Flaking Unit Description
1. Introduction to Flaking Unit
1.1 What is Caustic Soda Flaking?
Caustic soda flaking is like turning a liquid superhero into a solid sidekick. It’s a process that converts liquid caustic soda, a powerful alkali solution, into convenient solid flakes. This flaking makes it easier to handle and transport, saving the day for countless industries.
1.2 Importance and Applications of Caustic Soda Flakes
Caustic soda flakes are the unsung heroes in a wide range of applications. They’re used in manufacturing soaps, detergents, and cleaning products. They neutralize acidic waste streams and help purify water. They’re even used in the textile industry, as well as in the production of paper and aluminum. Basically, caustic soda flakes are the multitaskers of the chemical world.
2. Process Overview of Caustic Soda Flaking
2.1 Raw Materials and Feedstock
In the world of caustic soda flaking, the main raw material is, well, liquid caustic soda. This highly concentrated sodium hydroxide solution is usually derived from the electrolysis of salt. It’s like taking the power of salt and transforming it into something even more useful.
2.2 Flaking Process Steps
The flaking process is a bit like turning liquid into snowflakes, but without the chilly weather. It typically involves spraying the liquid caustic soda onto a rotating drum, where it solidifies and forms flakes. The flakes are then collected and dried, ready to save the day in their solid form.
2.3 Quality Control and Testing Procedures
Quality control is crucial in the caustic soda flaking unit. The flakes must meet specific purity and quality standards to ensure their effectiveness in various applications. Testing procedures, such as measuring the concentration and inspecting the flakes for impurities, help ensure that only the best flakes make it out into the world.
3. Equipment and Machinery in Caustic Soda Flaking Unit
3.1 Flaker Drum
The flaker drum is like the stage where the liquid caustic soda transforms into solid flakes. It rotates, allowing for efficient and uniform flake formation. Think of it as the drum set, creating a symphony of solid flakes.
3.2 Conveyors and Feed Systems
Conveyors and feed systems help move the caustic soda to the flaker drum. They ensure a smooth and continuous flow of liquid caustic soda, like a conveyor belt of superhero power, making sure flakes are formed without interruption.
3.3 Heat Transfer Systems
Heat transfer systems play a key role in the flaking process. They help cool down the liquid caustic soda and promote solidification. These systems are like the cool breeze that turns hot liquid into refreshing flakes.
See also Analyzing the Use of Caustic Soda as a Depilatory Agent in Cosmetics Industry
4. Operational Parameters and Control Systems
4.1 Temperature and Pressure Control
Temperature and pressure control are crucial to achieving the perfect flake formation. By keeping the conditions just right, the flaking process can be optimized and ensure consistent quality flakes are produced. It’s like finding the perfect balance of heat and pressure to create the ultimate flake masterpiece.
4.2 Flaking Rate and Throughput Optimization
The flaking rate and throughput are key considerations in the caustic soda flaking unit. By optimizing these parameters, the production efficiency can be maximized. It’s like finding the sweet spot between speed and quantity, making sure the flakes are formed at just the right rate.
4.3 Monitoring and Control Instruments
Monitoring and control instruments keep a watchful eye on the flaking unit, ensuring everything runs smoothly. These instruments measure and monitor various parameters, such as temperature, pressure, and flow rates. They’re like the superheroes with their super senses, making sure the flaking process stays on track.
And there you have it—a crash course in caustic soda flaking. From liquid to solid, this process transforms caustic soda into versatile flakes that save the day in countless industries. So next time you spot a caustic soda flake, remember the journey it took to become the chemical superhero it is today.
5. Safety Measures and Hazards in Caustic Soda Flaking
5.1 Chemical Hazards and Safety Precautions
When it comes to caustic soda flaking, safety should be your top priority. Caustic soda (sodium hydroxide) is a powerful chemical that can cause serious harm if mishandled. So before you jump right into the flaking process, it’s essential to understand the hazards and take appropriate safety precautions.
One of the primary chemical hazards associated with caustic soda is its corrosive nature. This means it can eat away at materials like metals, skin, and anything it comes into contact with. That’s why it’s crucial to wear protective gear, such as gloves and goggles, whenever working with caustic soda. Trust me, you don’t want to end up like a superhero gone wrong with burning skin or ruined clothing!
5.2 Personal Protective Equipment (PPE)
Speaking of protective gear, let’s talk about the superhero suit you need to wear. Okay, maybe it’s not exactly like a superhero suit, but personal protective equipment (PPE) is just as important. Along with gloves and goggles, you should also consider wearing a chemical-resistant apron and boots to keep yourself shielded from the corrosive effects of caustic soda. Safety first, folks!
5.3 Emergency Response and Spill Handling
Accidents happen, even to the best of us. So it’s important to be prepared for any caustic soda spills or emergencies that may occur during flaking. Have an emergency response plan in place, including procedures for containing and cleaning up spills. This may involve using absorbent materials or neutralizing agents to safely handle the situation. Remember, a little spill can turn into a big mess if not handled promptly, so be ready to spring into action!
6. Maintenance and Troubleshooting in the Flaking Unit
6.1 Routine Maintenance Procedures
Just like your car needs regular maintenance, so does your caustic soda flaking unit. Routine maintenance is essential to keep everything running smoothly and avoid any unexpected breakdowns. This can include tasks like checking for leaks, inspecting valves and pumps, and cleaning equipment. By keeping up with these maintenance procedures, you can ensure that your flaking unit stays in tip-top shape and avoids any unwanted surprises.
6.2 Common Issues and Troubleshooting Techniques
Sometimes, even with the best maintenance, problems can still arise. It’s important to be familiar with common issues that occur in caustic soda flaking units and the troubleshooting techniques to address them. Whether it’s a clogged line, a faulty temperature control, or an unresponsive control panel, knowing how to identify and fix these problems can save you a lot of headaches. So, channel your inner MacGyver and get ready to troubleshoot like a pro!
6.3 Preventive Maintenance Strategies
Prevention is better than cure, they say, and that holds true for your flaking unit too. Implementing preventive maintenance strategies can help you avoid costly repairs and downtimes. This can include regular equipment inspections, lubrication of moving parts, and implementing predictive maintenance techniques, such as monitoring system performance and analyzing data to identify potential issues before they become major problems. Remember, a little maintenance now can save you a lot of trouble down the line!
7. Environmental Considerations and Waste Management
7.1 Environmental Impacts of Caustic Soda Flaking
While caustic soda flaking may be a fascinating and crucial process, it’s important to consider its potential environmental impacts. Caustic soda is a highly alkaline substance that, if released into the environment without proper controls, can harm aquatic life and ecosystems. It’s vital to follow strict environmental regulations and guidelines to minimize any negative effects. Let’s keep things clean and green, people!
7.2 Waste Treatment and Disposal Methods
Waste not, want not. When it comes to waste generated during caustic soda flaking, it’s essential to have proper treatment and disposal methods in place. This may involve neutralization of waste streams, filtration, or other purification processes to ensure that any harmful substances are removed before disposal. It’s all about being responsible stewards of the environment and ensuring that our waste doesn’t come back to haunt us!
8. Future Developments and Advancements in Caustic Soda Flaking
8.1 Emerging Technologies in Flaking Processes
Caustic soda flaking isn’t stuck in the past! Exciting developments and advancements are constantly being made to improve the flaking process. From innovative designs to enhance efficiency and productivity, to automation and digitalization that revolutionize operations, the future of flaking is looking bright. Stay tuned for cutting-edge technologies that will make you say, “flaking has never been so cool!”
8.2 Sustainability and Energy Efficiency Improvements
In today’s world, sustainability is the name of the game. The caustic soda industry is no exception, with a growing focus on reducing energy consumption and environmental impact. Expect to see advancements in energy-efficient equipment, recycling of waste heat, and the exploration of more sustainable raw materials for caustic soda production. It’s all about finding ways to flake responsibly and leave the planet in better shape for future generations. We can all be eco-warriors, one flake at a time!
See also Strategies for Enhancing Brand Image and Reputation of Iranian-made Caustic Soda Products
In conclusion, the caustic soda flaking unit is a vital component in the production of caustic soda flakes, serving various industries with its versatile applications. By following proper operational procedures, ensuring equipment maintenance, implementing safety measures, and considering environmental factors, manufacturers can optimize the production process while minimizing risks. Furthermore, ongoing research and advancements in flaking technology present opportunities for improved efficiency, sustainability, and product quality. With a comprehensive understanding of the caustic soda flaking unit, manufacturers can ensure the consistent supply of high-quality caustic soda flakes to meet the demands of diverse industries.
FAQ
1. What is the purpose of caustic soda flakes?
Caustic soda flakes, or sodium hydroxide flakes, are used in various industries for a range of applications. They are commonly utilized in chemical manufacturing processes, water treatment, pulp and paper production, textile manufacturing, and as a cleaning agent. Caustic soda flakes are highly versatile and play a crucial role in numerous industrial processes.
2. Are there any safety considerations when working with a caustic soda flaking unit?
Yes, working with caustic soda flakes involves certain safety considerations. Caustic soda is a strong alkali and can cause severe burns or skin/eye irritation upon contact. It is essential to follow proper safety protocols, including wearing appropriate personal protective equipment (PPE), implementing spill response procedures, and ensuring proper ventilation in the flaking unit area. Manufacturers should also provide comprehensive training to employees regarding the safe handling and storage of caustic soda flakes.
3. How can the efficiency of the flaking unit be optimized?
To optimize the efficiency of the flaking unit, several factors can be considered. This includes monitoring and controlling operational parameters such as temperature and pressure, ensuring regular maintenance of equipment, implementing preventive maintenance strategies, and optimizing the flaking rate and throughput. By maintaining optimal process conditions and equipment performance, manufacturers can enhance the efficiency of the caustic soda flaking unit, leading to increased productivity and product quality.
4. What are the environmental considerations associated with caustic soda flaking?
Caustic soda flakes production involves certain environmental considerations. The waste generated, such as spent caustic solution or process residues, may require appropriate treatment and disposal methods to prevent environmental contamination. Manufacturers should adhere to environmental regulations and implement waste management strategies to minimize the impact on the environment. Additionally, there is ongoing research and development to explore more sustainable and energy-efficient flaking processes, aiming to reduce the environmental footprint of caustic soda production.
Hossein Moshiri
WA +989124311007
Comments
Post a Comment